Succeeding with remote operations means monitoring and servicing equipment, machines and other physical assets in the field, from a distance and without the need to dispatch field personnel.
Equipment builders, OEMs and service organisations are increasingly interested in methods to succeed with remote operations, now more than ever in a post COVID-19 world, where remote work and physical distance may be the norm.
For machine manufacturers, remote troubleshooting equipment without sending technicians on site can significantly reduce field support costs and travel time. For manufacturing companies it means their machine problems are identified earlier and solved more quickly, which improves their overall equipment efficiency (OEE).
The ABCs of remote operations – getting started with IIoT remote monitoring and control
Enterprises wishing to set-up remote operations for field assets will need to achieve three main milestones before seeing any benefits.
- Remote connectivity. The first milestone is ensuring the assets are sending operational data securely and at constant intervals, depending on the type of machine and on the business case.
- Remote monitoring. The second milestone is ensuring that this raw sensor data is processed to obtain relevant business indicators from it and insights on the machine’s condition or performance.
- Remote servicing. Finally, the third milestone is making those data insights actionable by using them to trigger remote automated service workflows, integrating with existing field support systems and helping technicians troubleshoot from afar.
You can’t have remote operations without the cloud
The start to any remote operation is taking machine data out of the local environment of the machine and making it available remotely (ie: outside of the plant, factory, building complex, industrial site etc.). This process will inevitably mean sending it over the internet to a cloud server. There may be differences from one use case to another in the type and amount of data being sent to the cloud, but you can’t have remote servicing & maintenance without making data available to outside teams.
Securing a data connection with the cloud is therefore essential, but it’s not straightforward. Industrial machines are sophisticated, high-value products with long lifecycles and legacy controller technology. Fortunately, industrial connectivity HW and SW providers such as HMS Networks and others are making it easier and faster than ever to connect machines and equipment to the cloud. They provide edge IIoT gateways and routers that connect to PLCs, HMIs or other industrial controllers, send machine data over the air and provide remote access to the PLCs via secure VPN connections.
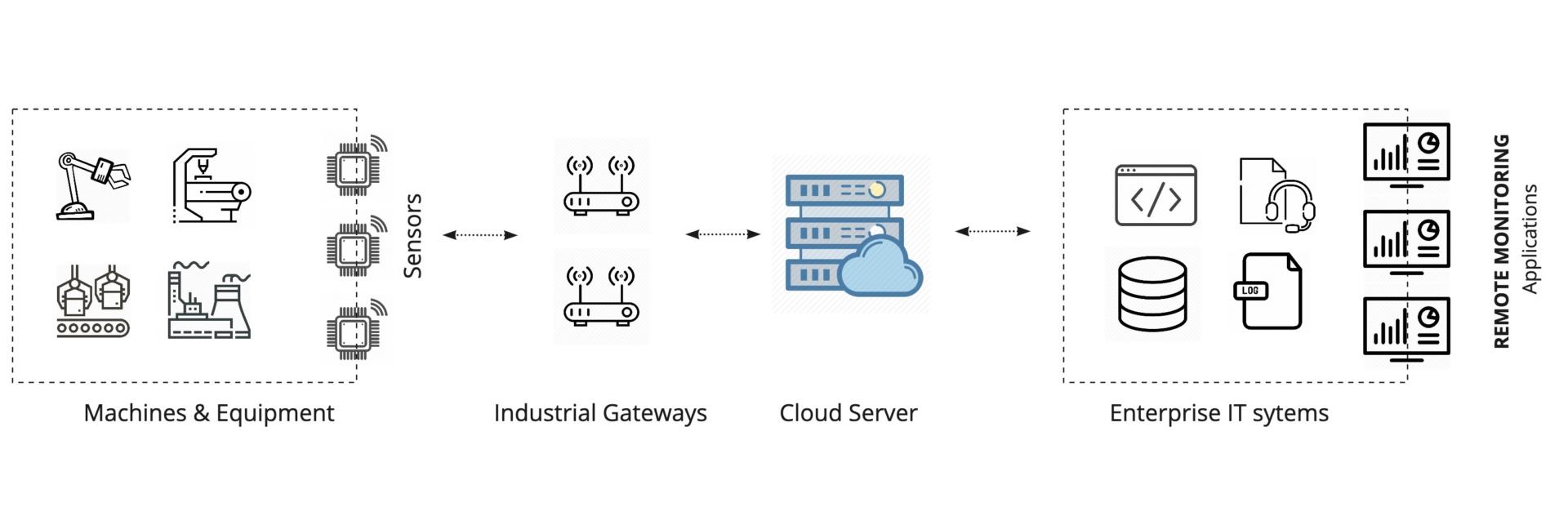
Service innovation is the holy grail of remote monitoring
Once a transparent connection to the machine is set-up and data starts coming in, remote operators and maintenance teams can start monitoring from a distance.
Connectivity-enabled monitoring and data collection may provide new information, but unless someone acts on it, there will be no effect on the equipment’s performance or processes and no direct value to customers. Only when the knowledge is turned into actions and detected issues are resolved will customers realise the benefit of remote monitoring machines.
So in order to optimise for better, faster and (ideally) automated actions, IIoT solution providers need to extend the technology stack with cloud data processing technologies such as data integration and automation. A purpose-built, cloud-native platform such as the Waylay platform perfectly complements any industrial connectivity solution.
The best example of why cloud data processing technology is needed to get the most out of your remote operations is in service innovation – improving after-sales support, field service & maintenance and offering personalised after-sales services to customers.
For these benefits to be achieved, the solution provider needs to put IIoT data in their business context, opening up permanent two-way communication lines between the IoT system and line-of business applications.
For example, a detected malfunction can then be immediately reported in the equipment manufacturer’s CRM system, where a support case is automatically created with all relevant fault information. The provider’s services team is empowered to take proactive action and reach faster problem resolution, leading to increase customer satisfaction.
Learn more
Equipment manufacturers and customers are facing a heterogeneous, geographically distributed device landscape that leads to high management and maintenance costs in the field. Service teams struggle to ensure maximum equipment availability while keeping costs of materials and labor to a minimum.
To reduce management and maintenance costs your customers need a solution for remote configuration and management for their devices.
At Waylay, we offer IIoT solution providers an IoT platform with built-in integration with IIoT gateways for easy data capture and a full set of software tools for automation, analytics and asset and process monitoring, that accelerate IoT solution development. Moreover, we provide a flexible visualisation dashboard that can be white labeled and templated to fit your end customers’ specific requirements.
We’d be happy to give you a free tour of the platform, sign-up for one over here.